In 1903, Ira Washington Rubel was considered as the first person to approach and apply offset printing technology on paper. Independent of Rubel, brothers Charles Harris and Albert Harris also discovered this and built offset printing machines for the Harris automatic printing company.
These are the two foundation marks that make up the strong development of this printing technology. After many ups and downs, in 1950, offset printing became the most popular printing technique for the commercial printing industry. In addition, after many improvements have been made to typesetting, ink and paper, optimizing print speed and life of typesetting, today, most printing, including press printing, use this technique. So what is offset printing and what processes does offset printing have to undergo to complete the print? Let’s learn more about this technique with HA AN!
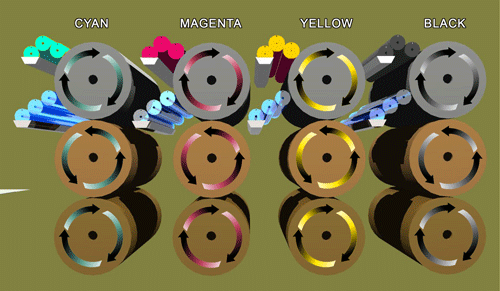
1. Offset printing concept in packaging production
Offset printing is a printing technique in which ink-stick images are pressed onto rubber sheets (also known as offset plates) and then pressed from this rubber pad onto the surface of the paper. When used with lithography, this technique avoids water staining the paper with the ink. Offset printing has many advantages, so it is very popular with manufacturers. Among the outstanding advantages include:
The image quality is high, sharp and cleaner than printing directly from the printout to the paper because the rubber pad evenly applies to the surface to be printed.
Application printing on many surfaces, including uneven surfaces (such as wood, fabric, rough leather).
Make offset prints easier
Prints last longer.
2. Offset printing steps in packaging production
2.1 Preliminary design
To get a quality, error-free offset printing, first you have to create a standard printout on a computer, or it can be understood as a standard print design file.
The information should be presented on the design in a harmonious way in terms of content, form and color according to the actual needs of businesses and customers. After agreeing and completing the design process, the offset printing unit can move to the next step, which is outfilm.
2.2 Output film
After the prepress design is completed, the printing technician will publish for outfilm. For prints with images, the film will be out into four sheets representing the four color layers C (Cyan), M (Magenta), Y (Yellow), K (Black).
The CMYK color system is the primary color system that can be dithered to create all other colors. The necessary colors are combined from 3 of the 4 colors mentioned above or all 4 colors with different parameters will achieve many different color results. This process is called “output of 4 films”.
2.3 Zinc plate exposure
After having 4 films, the printing technician will dry each sheet one by one on the zinc plate or in a simpler way, take pictures of each film on each zinc plate with a zinc drying machine. This is the third step in the offset printing process.
2.4 Offset Printing
In the offset printing process, the technician will print each color one by one, the arrangement of the front and back of each type of printing color will depend on the technique and experience of the technician.
First, the printing technician will choose one of 4 colors to install on the offset printer batch. In the ink input part of the machine, the technician will also give the corresponding ink. For example, C color zinc plate (Cyan), the technician also gives C ink and proceeds to print. The roll that rotates over the paper will knock the printing element onto the printing paper.
After running all the printing quantities, the technician will remove the zinc, clean all the old ink, install the new zinc, put the new color printed paper in and continue the old process. The process proceeds sequentially until all 4 colors are exhausted, those 4 colors are printed on top of each other to produce the final print.
During the printing process, the print technician will have to run drafts to ensure stable printing colors. When conducting offset printing, the printer must deduct paper loss to ensure quality.
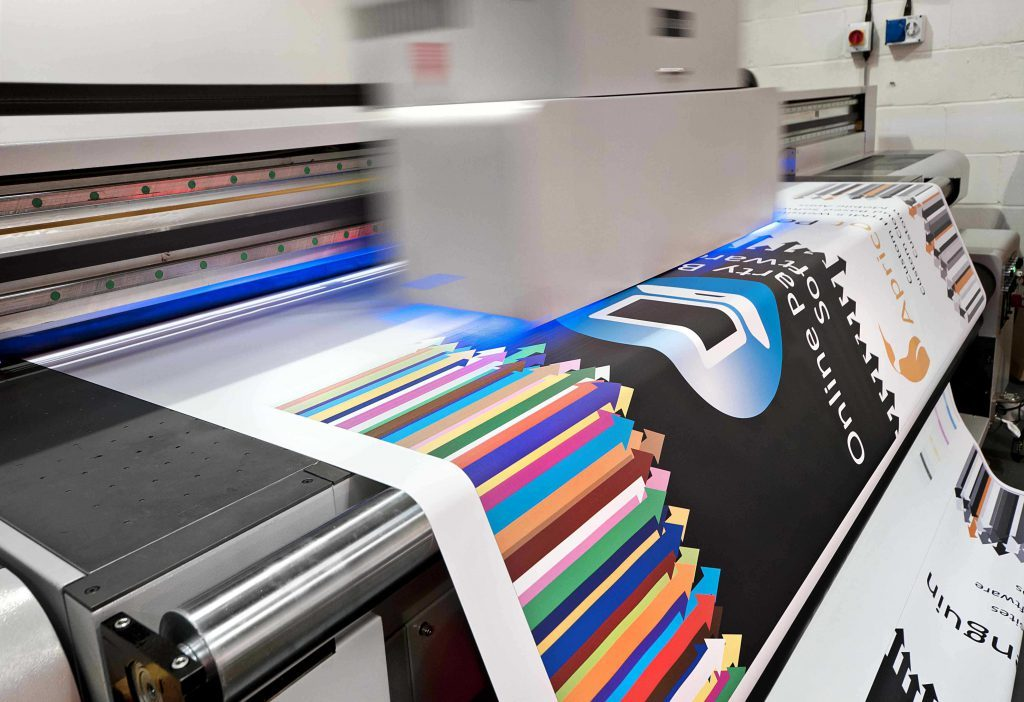
2.5 Machining after printing
After offset printing, the printing technician will carry out the final step to perfect the offset print, which is the post-printing processing process. Usually, the post-printing process that is widely used is the matt lamination and glossy lamination process. In which, matt lamination will create a smooth and soft surface. Polishing will give the surface a glossy finish.
Matt lamination is the process of embellishing the product and is not required to be processed, depending on the customer’s wishes. Matte lamination is laminating a thin film on the surface of the leaflets after printing, the matt lamination will make the leaflet printing smooth and help the images become eye-catching. To ensure that the offset printing process does not have errors and must be reprinted, the printing technician must be really meticulous in the steps to create quality prints.
(Source: Collector)
To get printing products, packaging with the best and modern offset printing technology.
Please contact Ha An via: Ha An Printing Joint Stock Company
Email: business@inhaan.vn
Phone: 024 625 36492 – 0985.649.304